Photo courtesy of Huntsman Building Solutions.
"Paralyzed by plenty, we find that endless options often lead not to freedom, but to indecision." Polyurethane Coating Floor
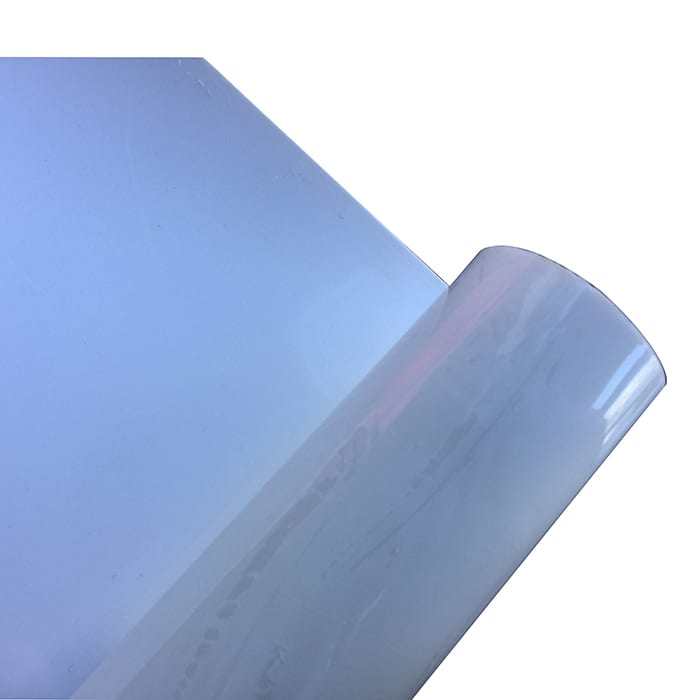
This anonymous quote embodies the feelings of many building managers and owners, as well as architects and engineers, when selecting a low-slope roofing system. Whether single-ply or multi-ply roofing; thermoplastic or thermoset; asphaltic or modified asphaltic; sprayed-on foam or liquid-applied; or a green, cold, or cool roof, the available choices seem endless. The simple truth is that there is no one answer. The best low-sloped roofing system depends on a variety of factors and variables that are project specific. All roofing systems have their unique advantages and disadvantages that should be weighed and understood during the design development phase. Some of these factors include but are not limited to:
Prior to the 1960s, there were only multi-ply roof systems: systems composed of multiple sheets or layers that are adhered together and predominantly composed of asphaltic-based membranes. In the early 1960s, a transformation took place with the development of ethylene propylene diene terpolymer (EPDM) in Germany. The discovery of an extremely durable, synthetic rubber revolutionized low-slope roofing by enabling a single-membrane roofing system comprising a single flexible sheet or layer of synthetic polymer, to equal the durability and impermeability of a multi-ply system. Single-membrane roofing technology advanced even further when, in 1966, another German company developed polyvinyl chloride (PVC) roofing membranes, which were fused to create a continuous roof system. In the 1980s, energy-efficient, ultraviolet- and puncture-resistant thermoplastic polyolefin (TPO) roofing systems were introduced. Additionally, liquid-applied roofing was developed in the 1980s. This system allowed for waterproofing by application of a hydrophobic liquid roof coating.
Roofing system technologies continued to evolve with the development of environmentally-friendly green roofs, which can be installed over nearly any type of roofing membrane. In addition to their higher insulation value, they reduce stormwater runoff and provide urban habitats for plants and animals. Yet another major milestone in the evolution of low-sloped roofing has been the introduction of PV (photovoltaic) solar panels, which allow for energy generation.
A trend gaining popularity is cold roofs, which are sometimes referred to as cold deck roofs. This system has insulation sitting directly on top of the finished interior ceiling with an air gap between the insulation and the roof deck above. This can reduce cooling costs by up to 30%. Cool roofs, on the other hand, are specifically designed to reflect more sunlight, and also are designed to shed heat by giving off infrared radiation through a phenomenon called “thermal emittance” and keep the roof temperature approximately 50 degrees Fahrenheit cooler. This reduces air conditioning and energy demand.
With all these options, how is an owner able to understand the right system for their roof? Here is an easy to-navigate, pros-and-cons summary, with red meaning poor, yellow being fair, and green being good.
Built-up roof systems (BUR) are the oldest of all low-slope roofing systems and hold the longest proven track record. Built-up roofs are composed of multiple roofing layers, providing inherent redundancy and a life expectancy of 15 to 30 years. Additionally, they require little maintenance and accommodate a variety of surfacing materials, such as gravel or pavers, which protect the roof system from UV radiation. Weather is an important factor when considering BUR, as they can become brittle in cold weather, fluid in hot weather, and have little resistance to fatigue. Due to the installation of multiple layers of roofing material, they require skilled labor, and their performance is contingent to the quality of installation.
Modified bitumen roofing is another asphaltic, multi-ply roofing system. It provides improved weather and temperature resistance compared to built-up roofing. When modifiers are added to the membranes, they increase their durability and flexibility. Since they are factory-manufactured instead of assembled in-situ, they have fewer inconsistencies as a finished product. Being petroleum-based (versus thermoplastic and thermoset roofing) like BUR, modified bitumen roofing is considered less eco-friendly and more vulnerable to increasing product cost. It also has a slightly shorter lifespan than BUR, typically lasting 15 to 25 years.
Single-membrane EPDM roofing is considered more low-cost, installer-friendly, and easier to repair than other roofing systems. However, because it is thermoset, it cannot be heated to make the adhesive-bonded membranes monolithic. Consequently, the waterproof integrity of this system depends on the quality of the installer, as the seams are prone to failure if not properly sealed. An EPDM membrane is not typically reinforced, making it vulnerable to punctures. If environmental impact is an essential consideration, EPDM has low reflectivity due to its dark grey color, which contributes to heat absorption. Yet perhaps, more importantly, EPDM can only be downcycled to be re-used as filler, not recycled. EPDM has a life expectancy of 20-30 years, with some manufacturers offering a 20-year warranty.
Unlike EPDM, thermoplastic membrane roofing can be re-heated and made monolithic, thus forming seams that are less vulnerable to deterioration. Thermoplastic membrane roofing systems also do not depend on the use of adhesives and offer additional means through which they can be adhered to the roofing substrate. Their single, lightweight membrane is composed of three factory-assembled layers, giving it the redundancy of multi-layered roofing systems. Their highly reflective surface allows solar energy to reflect, which causes sunlight to reflect; this can be a nuisance to taller buildings nearby. These systems require more equipment during installation, but a 35-year system warranty is available.
PVC is a very flexible and easily welded thermoplastic membrane. It tends to grey over time, which creates low reflectivity and can produce hazardous smoke in a fire. Relative humidity is an important factor when considering a PVC roofing system, as it is prone to algae and mildew growth. However, these issues can be addressed by adding biocides to the PVC. Another negative aspect of PVC roofing is that the liquid plasticizers added to it during manufacturing are slowly lost over time through evaporation, causing the sheet to become brittle with age.
PVC embrittlement issues were resolved in the development of a different type of PVC roofing, called PVC-KEE (Ketone Ethylene Ester), which is regarded as a more premium product. The plasticizers added are both liquid and solid, with only the liquid deteriorating over time, ensuring long-term flexibility of the membrane. The KEE roofing system, despite its name, is governed by a different specification than PVC-KEE. Its high-polymer content ensures not only greater flexibility, but better long-term weathering compared to other roofing systems. Chemically resistant to oils and grease, this is a good option for roofs that expect to house numerous mechanical units. However, KEE does come with a higher cost, and its long-term performance is dependent on skilled installers.
TPO is considered an economical thermoplastic option and is one of the fastest growing roofing systems. Known for its excellent performance, TPO is lightweight, but most importantly, it is inherently flexible and can be heated and shaped repeatedly. It contains no plasticizers to evaporate, thus it will not become brittle over time, enabling TPO to be less vulnerable to tears. It is resistant to UV rays and chemicals, as well as algae and mildew growth. Sustainability-wise, TPO is recyclable, as well as energy-efficient due to its reflective properties. It has no chlorine, which is a chemical concern for green initiatives. Additionally, TPO is slightly stiffer than PVC, making detailing more difficult during installation and requiring experienced installers. TPO membranes only have a lifespan of 10 to 20 years.
Spray polyurethane foam (SPF) is a lightweight, seamless roofing system that provides excellent waterproofing and insulation. However, it requires specialized equipment and skilled labor for installation, and tends to be vulnerable to punctures. SPF offers little to no protection against the sun’s UV rays, but this can be addressed by applying an elastomeric roof coating to achieve the necessary level of UV protection. While the installation costs are comparable to many other commercial roofing systems, their lifespan of 15 to 25 years is directly dependent on recurrent maintenance and recoating.
Liquid-applied roofing cures into a solid, monolithic, multi-layered, fleece-reinforced roofing system compatible with a broad range of substrates, such as concrete, wood, and metal. It has long-term performance and offers the redundancy found in other multi-layered roofing systems. By being self-terminating, it does not require counterflashing or termination bars. It is considered to be a sustainable system by having VOC compliance and containing no isocyanates, which can cause health issues. If the health impact of installation to building occupants is a consideration, liquid-applied roofing creates low odor and cures in ambient temperatures, which precludes the use of pungent adhesives, the noise of fasteners, or the odor of torch-applying the system. However, it is important to be aware that liquid-applied roofing has its limitations with respect to humidity and outdoor temperature, which can elongate the timeline for installation. Additionally, preparation of the substrate is critical for performance, relying on the quality of the installers.
With all the possible options and combinations in roofing systems, it is of the upmost importance to consider the existing conditions, consult with a design professional, and obtain insight and recommendations from roofing manufacturer representatives. There is not an all-encompassing, one-size-fits-all solution, but there are options based on the existing conditions and ways to maximize an owner’s return on investment when considering a replacement low-slope roof.
In the end, the best roofing system for your building is the one that best meets your financial and maintenance priorities, the roof’s intended exposure or use, and the existing environmental conditions present at the building’s location.
Sergio Silveira is a registered architect with more than 30 years of experience leading large design and construction projects. He is a Building Sciences Practice Leader at Rimkus, a leading global engineering and technical consulting firm. Prior to joining Rimkus, he served as assistant commissioner in charge of several New York City capital programs.
Mike Lopez is director, technical services, on the Rimkus Built Environment Solutions team. He has extensive experience in building envelope consulting and construction administration, specializing in exterior restoration, waterproofing, roofing, and leak remediation. He is a registered architect, a member of the American Institute of Architects, and holds an NCARB certificate (National Council for Architectural Registration Boards).
You must have JavaScript enabled to enjoy a limited number of articles over the next 30 days.
This webinar is a must-attend for all roofing contractors who are looking to understand market insights related to current and future installation trends.
This intensive 2-day conference presents new and improved ways to run your roofing business for both commercial & residential applications. Gain invaluable knowledge from experienced industry leaders presenting sessions geared to help you improve your business and engage in exclusive networking opportunities with your peers at Best of Success.
Copyright ©2024. All Rights Reserved BNP Media.
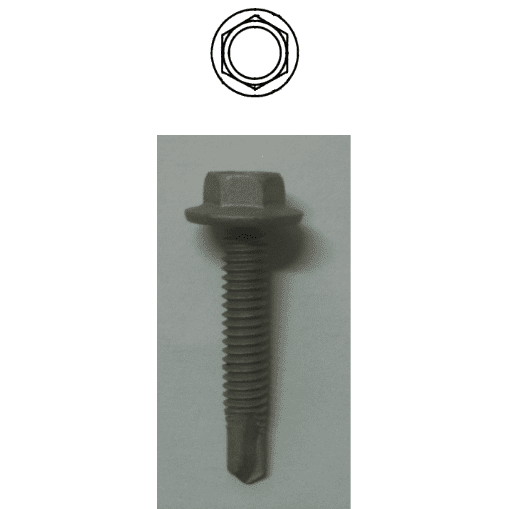
Waterproofing Coating Design, CMS, Hosting & Web Development :: ePublishing